Water chillers can be used in many ways, for different things. Pharmaceuticals, food production, petrochemicals, plastic production, metal plating, or agriculture, are some of the industries that benefit from these machines, for their manufacturing processes. Some may employ water chiller for:
Cover Area Cooling
When you are manufacturing something, the equipment generates a lot of heat. This creates a hot environment that might be dangerous to employees.
A cover area cooling unit can cool the air in a factory, making it safer and even comfortable for workers. These air-cooling systems can also keep offices, and other working spaces cool during warm weather.
Process Cooling
Industrial processes create heat through friction, equipment, or burning. This can shorten the lifespan of the equipment, however, you can increase their longevity and keep the processes running smoothly by utilizing a process chiller.
Unlike standard HVAC systems, process chillers cool a liquid that circulates the area to be cooled, thus maintaining a set temperature. The liquid may be either water, propylene, ethylene glycol, methanol, or even ethanol.
Since processes can be quite diverse, some coolers may have different forms. The cooled liquid circulates the equipment to keep it at a safe operating temperature, or it can cool it to a lower temperature for a process.
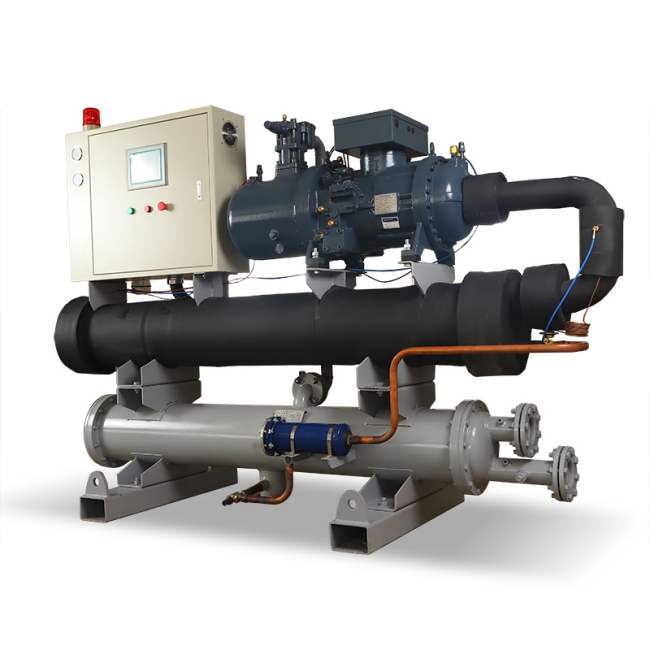
Plastic Manufacturing
Plastic is extremely temperature-sensitive, melting in a hot environment. During production, plastics need to cool in molds to an appropriate temperature.
Cooling the molds requires a hard-working chiller. For extruded plastics, the formed plastic needs a cooling bath to chill, thus the role of the chiller.
For extrusion plastics production, a great setup includes a second heat-exchanger to separate the water used for cooling the equipment and the extrusion water. Keeping these waters separated is crucial as plastic can contaminate the extrusion water.
Metal Plating and Anodizing
Metal plating can be achieved with electroplating or electroless plating, both of which require high temperatures. Anodizing is a similar process to reduce corrosion on non-iron surfaces, and it also requires high temperatures.
This leads to companies relying on heavy-duty chillers to remove the heat produced from the solution. The heat can be removed by sanding the plating or anodizing liquid to a heat exchanger. Another method involves the use of glycol or water-containing coils to cool the fluid in the tank.
Food Processing
Chillers are an essential part of the food industry. Glycol coolers send chilled propylene glycol through cooling coils for chilling food or beverage store units.
Breweries and wineries often use glycol chillers for keeping their products at the right temperatures. Food manufacturers use process coolers to chill dough mixers or cool ice cream makers.
The information is provided by the air-cooled chiller manufacturer.